
1. Morton Effect in 23,000 HP Compressor Causing Vibration-Induced Shutdown
By Nelson L. Baxter, President of ABM Technical Services, CVA Cat IV, R.P.E.
Abstract: Large centrifugal compressors that are utilized in the process of producing compressed gases or liquid nitrogen, oxygen and argon are located all over the world. There are thousands of these large compressors in operation. These machines are unique in design and thus have some interesting problems. This paper presents a case history of a problem that occurs in this category of rotating equipment. This case illustrates how advanced analysis equipment can be utilized to capture amplitude and phase deviations, compressor surge and torsional responses from both start up transients and the torsional magnetic pole slip stimulus from synchronous motors.
Introduction: There are different centrifugal compressor designs. They are powered by either an induction motor or a large synchronous motor. The machine in this paper is of the basic arrangement described as follows. Synchronous motors are fairly common on the larger units because they can be used to control the power factor, thus reducing the cost of electricity. The motor drives a large bull gear at typically 1200 or 1800 RPM.
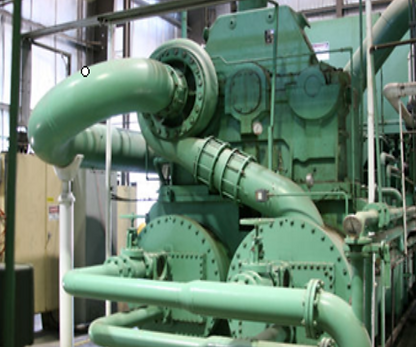
The bull gear drives the pinion shafts which have an impeller on either one or both ends. The diameter of the bull gear is several times that of the pinion shafts so the impeller speeds are several times the speed of the input shaft. The bearings are a tilt pad design. Aluminum labyrinth seals provide the shaft sealing. On the bigger compressors, the span between the motor and the bull gear will often be several feet in length. All of these design features play a key role in the vibration response of these compressors.

Bull gear driving small diameter pinion. This photograph is from a four-stage machine. Stages one and two are in the foreground with stages three and four in the background.
Morton Effect in 23,000 HP Compressor Causing Vibration-Induced Shutdown
The vibration level on the Stage 3X, 3Y, 4X & 4Y probes of a large compressor, like the one seen here, would begin to oscillate. The time period of the oscillations varied from 6 to 7 minutes.
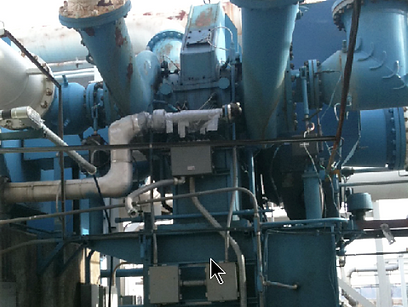